FS事業(事業化可能性の調査)
- TOP
- FS事業(事業化可能性の調査)概要
- 課題別 事例
- 超零細 樹脂成型工場へのロボット導入
組立/樹脂押出成形品
実施概要
支援先中小企業のニーズ・課題
株式会社中村屋は、主に住宅建材関連の樹脂押出成形品を製作している会社であり、社長とその奥様と2名ほどのパートタイマーのみで運営している工場である。社長の中村氏は大手樹脂メーカから独立し押出成形の突出した技術力と金型設計から一貫して対応できるという特色を持ち、大阪地域の押出成形業界で知らないものはいないと言われている。
(株)中村屋で扱っている製品の中で住宅用ユニットバス施工時の補強材として図1のような樹脂部品があり、現在、これを押出成形によって製作している。図2のように押出成型機ラインから切断されて排出されてくる。
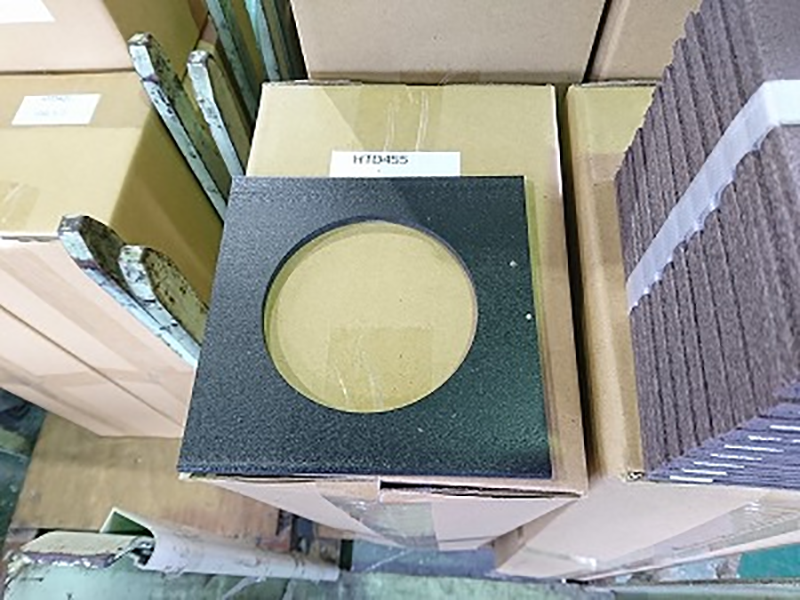
図1
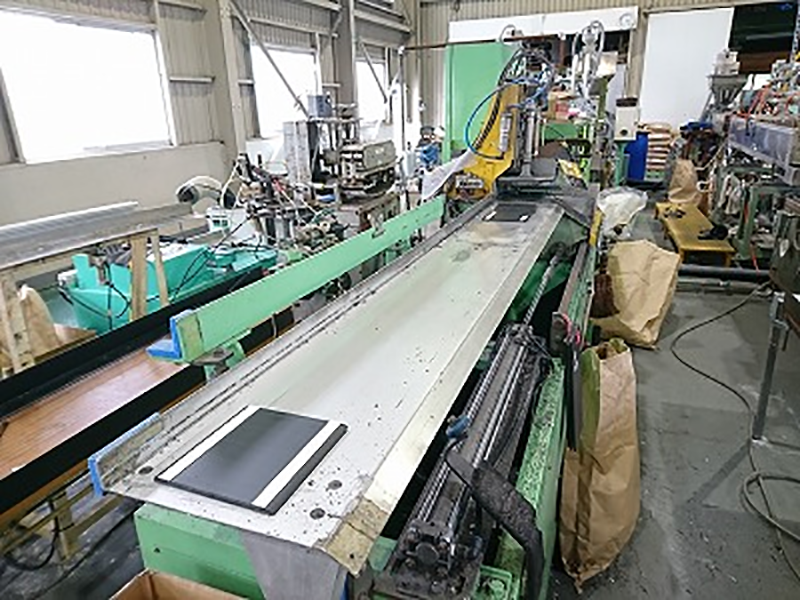
図2
今回の対象ワークは図1で示したように穴あけ加工が必要であるが、φ30の穴あけ加工は図3のようなホールソーを装着したボール盤でパート作業者が行っている。 毎月2,000枚ほどを加工する単純作業でありこの作業に手を取られている。また、φ80、φ100の直径の大きな穴は割れやすいため外注加工に頼っている。よって、本作業の自動化、外注加工費の削減が望まれている。
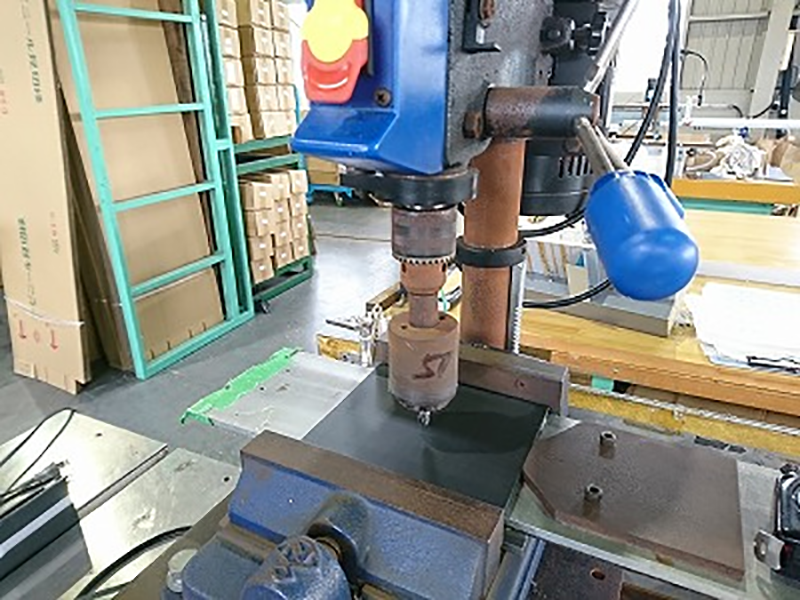
図3
課題の解決方法
課題を解決する方法として、現在は手作業で行っている当該樹脂部品の穴あけ加工を、ロボットを使って自動化する。すなわち、押出成形機から出てきた樹脂部品を検品の上、マガジンのようなものにセットし、ロボットシステムによって穴のサイズを自由に変えて穴あけ加工を行う。また、ラベル張りなども併せて行うことで成型機から梱包までの人手作業を極力なくすことが可能となる。
FS実施内容
本作業のロボットによる自動化にあたって、ロボットによる穴あけ加工が適切に行えるかが課題である。樹脂部品の素材はポリスチロールと呼ばれる発泡系素材であるため割れやすく、ロボットによる位置制御、移動速度、加工時間などを検証し、実践導入への可能性を探るために、実際に協働ロボットを使った穴あけ加工の実験をFSとして実施した。
(1)エンドミル加工治具の設計・製作
樹脂部品の穴あけ加工の手法は、ホールソーを使う方法もあったが、ロボットのティーチングで穴径を変更できるメリットを活かすために当初予定通りエンドミルで行うことにし、協働ロボットに取付ができるエンドミル加工治具の設計・製作を行った。ロボットにはUniversal Robot社のUR5eを使うことにした。
エンドミルを回転させる主軸モータとして、オリエンタルモータのブラシレスモータBMUシリーズを使うことにした。モータ出力は60Wで、専用のコントローラで80~4000rpmまで回転速度を可変することができる。また、エンドミルは、φ10mmとφ5mmの2種類を用意することにした。
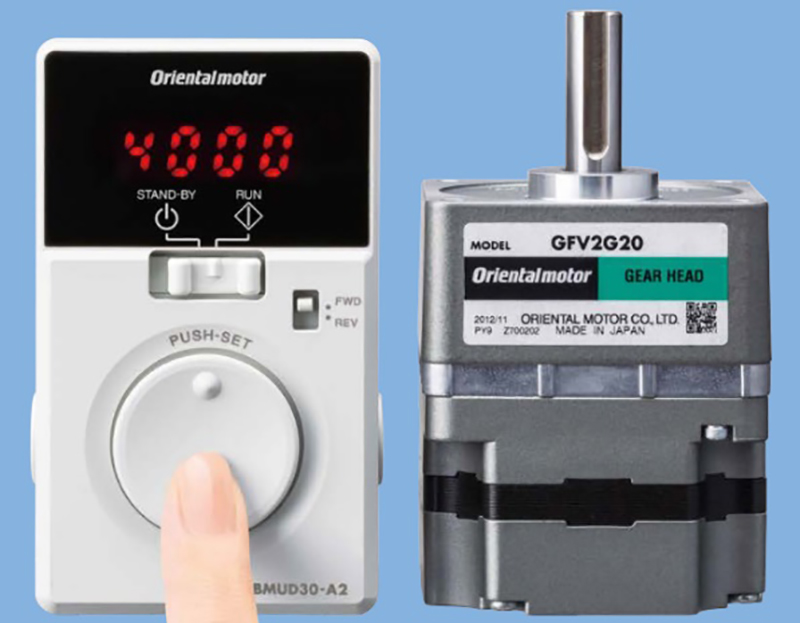
オリエンタルモータ BMUシリーズ
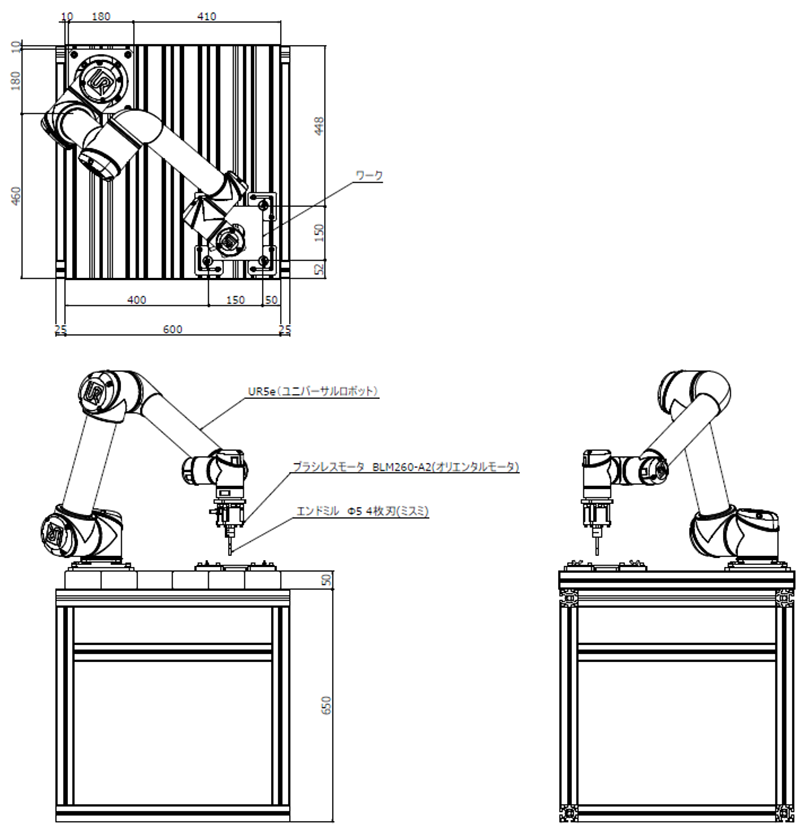
(2)加工実験
協働ロボットにエンドミル加工治具を装着し、穴あけ加工の実験を実施した。
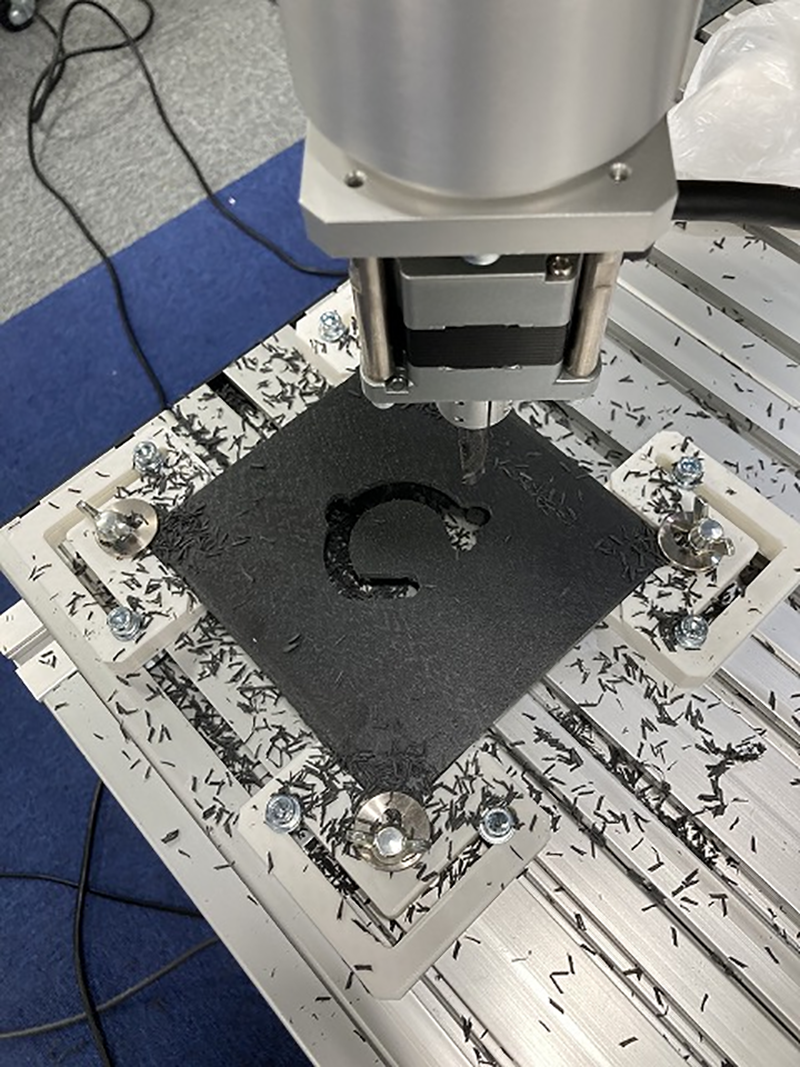
加工実験の様子
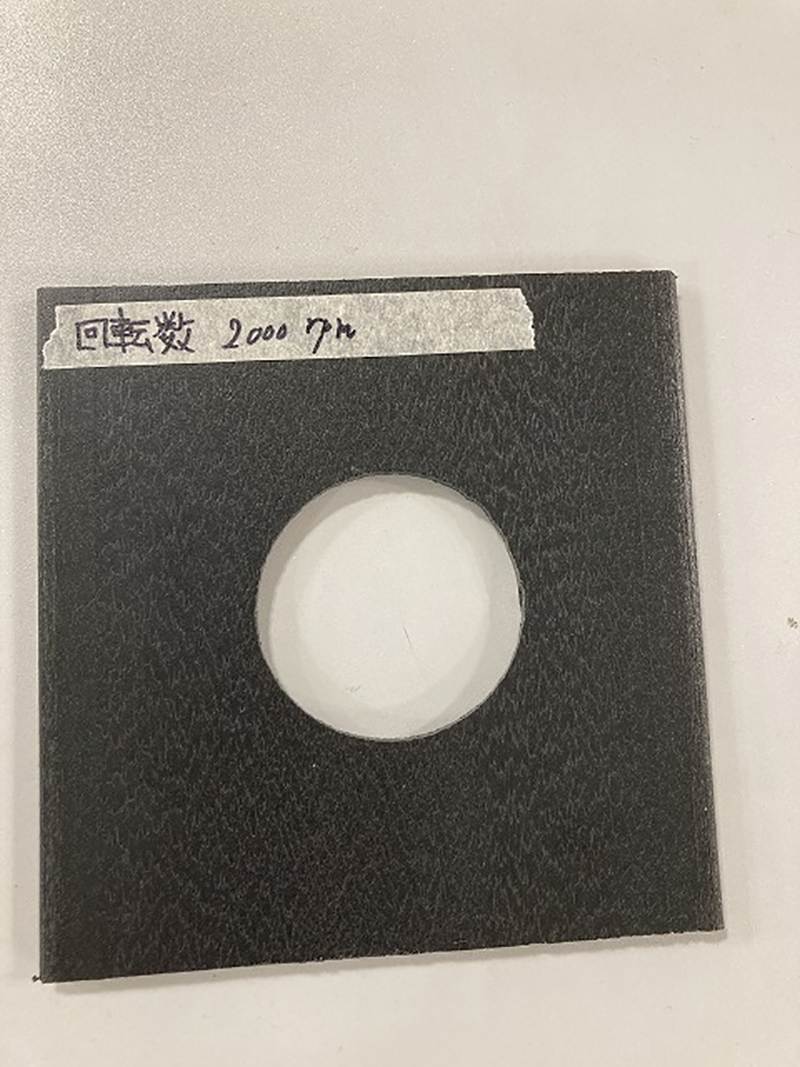
加工済みワーク
当初、エンドミルはφ10mm を使っていたが、協働ロボットにかかる負荷が130Nにも達し、協働ロボットの安全システムが働いてしまうため、エンドミルを φ5mm に変更した。結果、切削抵抗が減ることによりロボットにかかる負荷は30Nに減少した。
加工時間は、実験当初1分15秒ぐらいであったが、エンドミルの回転数やロボットのティーチングを工夫することで最終的に30秒ほどまで縮めることができた。
エンドミルの回転数は、切削抵抗を減らすために高回転(4000rpm max)の方がいいことがわかったが、一方、熱が発生してしまい樹脂が溶けてエンドミルに固着してしまう現象が見受けられた。よって、一度に深く削るのではなく、複数回に分けてだんだん深く削っていき最後に貫通させる手法によって回避した。
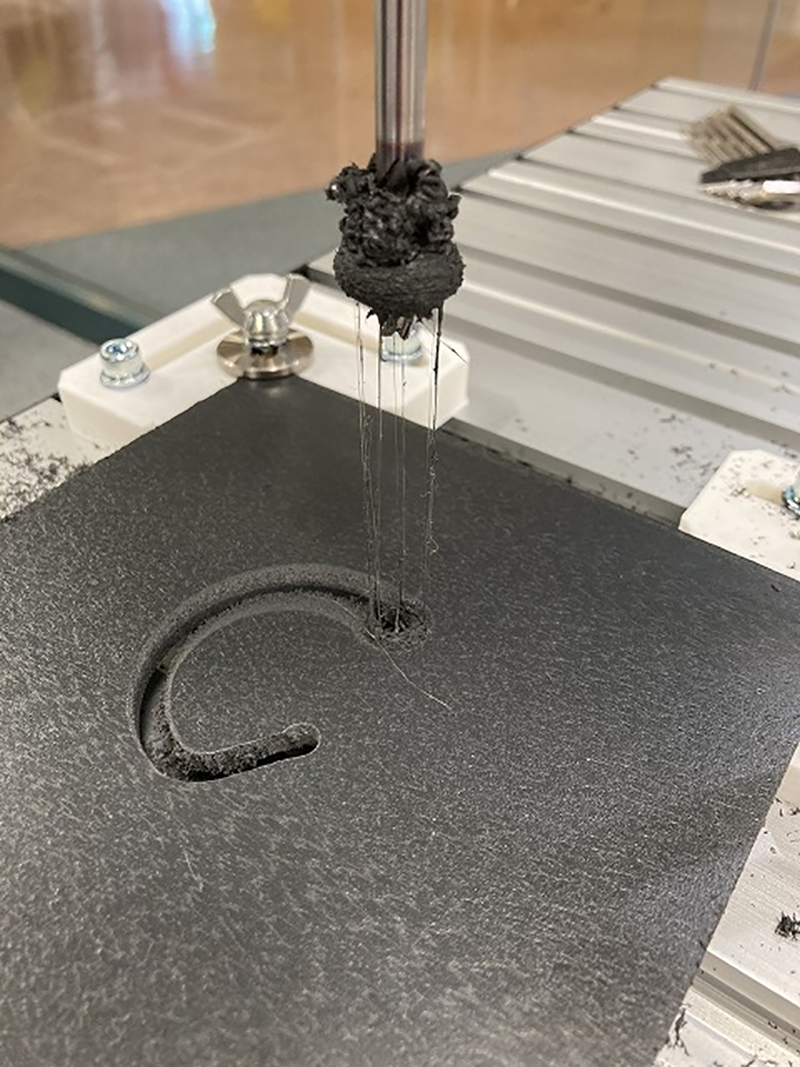
樹脂が溶けて固着した様子
得られた知見・成果ならびに事業化への課題
今回のFSでは、協働ロボットによる樹脂部品への穴あけ加工を行うという課題に対して、エンドミル加工治具を設計・製作し、実際のワークを使って加工実験を行った。
加工時間をなるべく短くし、なおかつ、熱による固着を避けるために、エンドミル径、エンドミル回転数、ロボットティーチング、切込み量(深さ)などをいろいろ試行した結果、以下の条件を導き出した。
・エンドミル径: φ5mm
・エンドミル回転数: 4,000rpm
・切込み量(深さ): 3回に分けて堀進む
・ティーチング: 送り速度24mm/s
この加工条件で、タクトタイムが約30秒となった。
また、今回の加工実験から次のような課題もわかってきた。まず、切削面の荒さ、形状が不安定(品質に問題あるかどうかは不明)ということである。切込み量(深さ)を3回に分けているため、切削面が段状になる場合があり安定しないという点である。
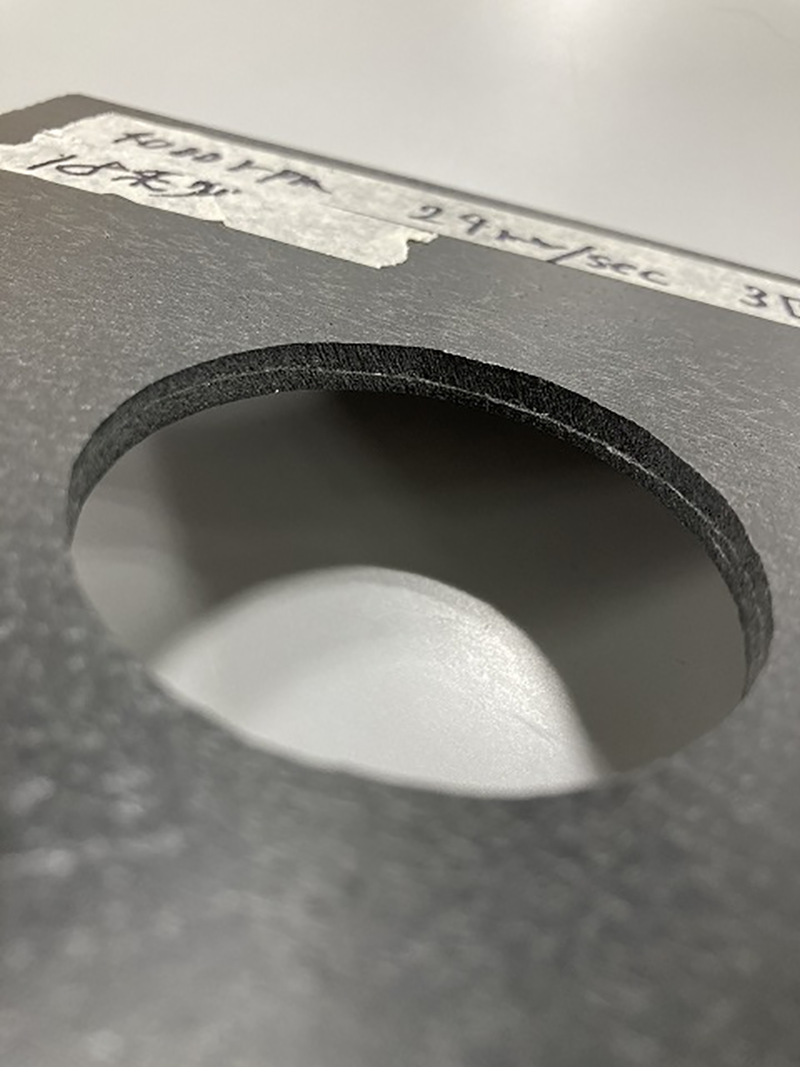
切削断面の様子
また、今回は加工条件によって熱による固着の問題を回避はしたが、ちょっとした条件の変化で発生する可能性もあり、さらなる検証が必要かと思われる。最後に、タクトタイム(現状30秒)も工場に実践投入したときに問題ないかの検討が必要である。
FS実施後の状況、今後の展望
FS実施後、加工実験の次の段階として、実際に工場へ導入する際のロボットシステムとしての構想設計を実施した。
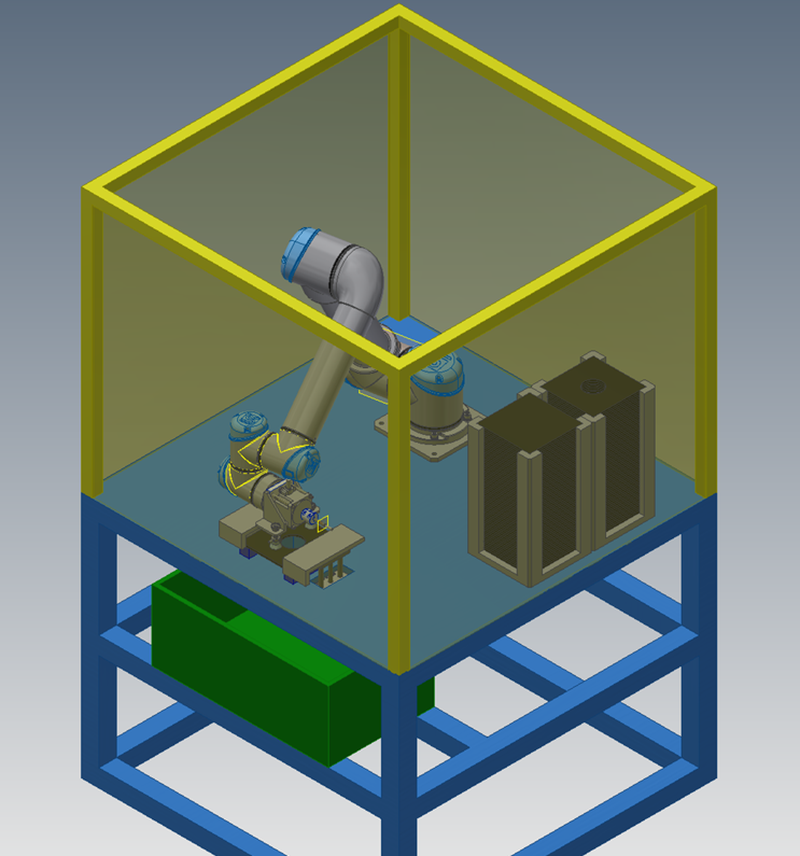
穴あけ加工ロボットシステム
穴あけ加工だけでなく、ワークのハンドリングもロボットにさせることで、マガジンにワークをセットすれば、あとは自動的に加工が行われるロボットシステムである。 このロボットシステムを工場に導入できれば、この作業にかかっていた作業者の削減と大型穴径の製品の外注加工費を削減することができる。さらに少人数で運営している工場の生産性向上と新製品開発への時間投資が可能となる。
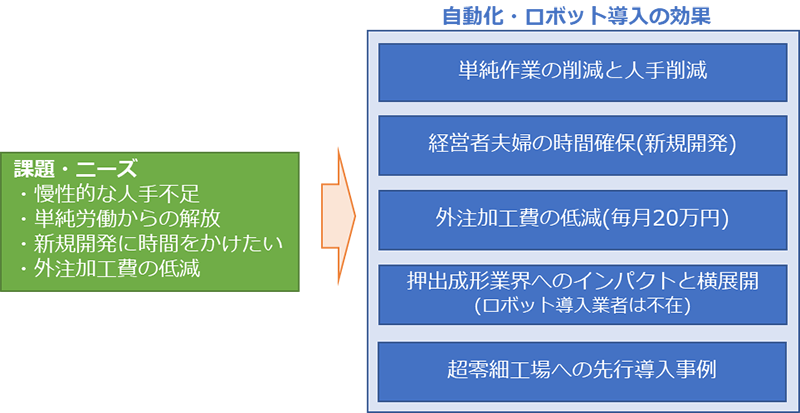
SIerとしてFS実施後の事業展開
一般的にロボットの導入は大手企業や中堅企業がほとんどで、中小零細企業への導入はなかなか進んでいない。そういう状況の中、今回FSを実施した(株)中村屋へのロボットシステム導入が実現すると、小規模工場への先行導入事例としてPRすることができ、ロボット未活用領域への訴求によってロボットシステムの販路拡大につながるものと思われる。特に中村社長は大阪府下の樹脂成型業界では著名な人物であるため、樹脂成型業界での横展開が期待できる。
ものづくりDXソリューションについて
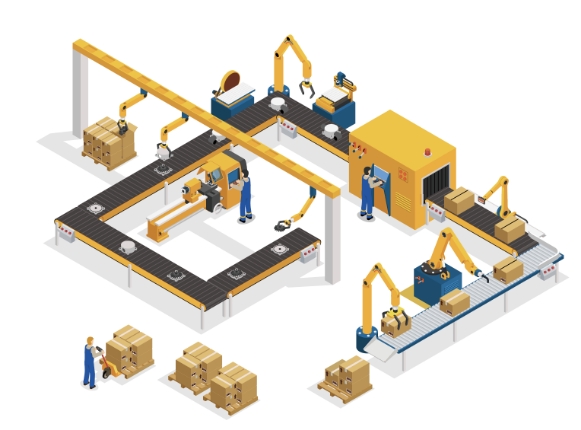
製造現場の課題を「ものづくりDXソリューション」の力で解決します。
現場労働力の不足、SIer・FA・ロボットエンジニアの不足、要素技術の高度化、IoT Industry4.0への対応など、製造現場にはさまざまな課題が山積しています。ひとつひとつが絡み合って複合的な課題となっていることが多く、どれかひとつを解決するといったことが難しいのが現状です。
そうしたものづくり現場の課題を「DXソリューション」の力で解決します。
提供メニュー
ご相談・お問い合わせ
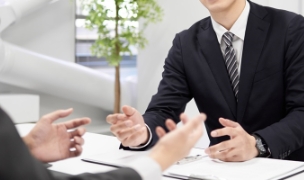
ロボット・AI・IoT・5Gなどを活用して、製造現場の自動化を目指します。
・ 省力化、省人化してコストダウンしたい
・ 生産性アップして売上を上げたい
・ 人的ミスを減らして品質価値を高めたい
・ どのメーカーの装置、ロボットを使えば効率的かわからない
・ 事例を知りたい
※貴社からの直接のご相談でも、連携している商社さんを通してのご相談でも構いません。
相談料/初回無料